UV Curable Ink: The Future of UV DTF Printing is Here
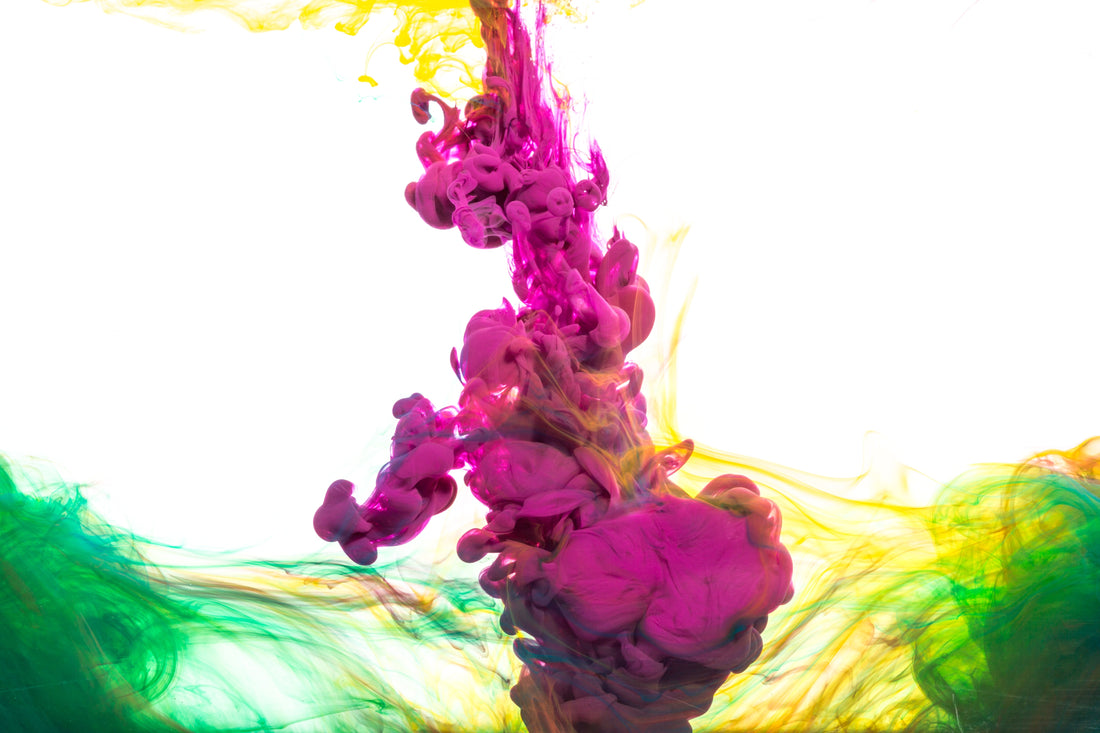
Ultraviolet (UV)-curable inks are a special type of ink that cure and dry through exposure to ultraviolet light. These inks offer several advantages over traditional solvent-based and water-based inks, making them a popular choice for a variety of printing applications.
Key Takeaway
- UV-curable inks cure and dry through exposure to ultraviolet light rather than through evaporation or absorption like traditional inks.
- They contain photoinitiators that release free radicals to trigger polymerization when exposed to UV light, transforming the ink from liquid to solid.
- Main components are monomers, oligomers, photoinitiators, and pigments. Additives are also used.
- Advantages include instant drying, superior print quality, versatile substrate compatibility, durability, and lower VOC emissions.
- Used for diverse applications like signage, labels, packaging, commercial printing, 3D printing, electronics, and more.
- Curing methods include mercury arc lamps, UV LED, UV laser, and e-beam curing.
- Formulating UV inks requires balancing viscosity, curing speed, adhesion, flexibility, and other factors.
- Limitations include higher costs, toxicity, surface curing limitations, and substrate restrictions.
- Future trends include inkjet optimization, LED curing, sustainable raw materials, smart inks, and hybrid formulations.
How Do UV Curable Inks Work?
The key difference between UV-curable inks and traditional inks is the curing process. Traditional inks dry either through evaporation of the solvent or absorption into the substrate. UV-curable inks, on the other hand, cure through a photochemical process initiated by UV light exposure.
UV-curable inks contain photoinitiators which are sensitive to UV light. When exposed to UV radiation, these photoinitiators release free radicals which trigger polymerization of the monomers and oligomers in the ink. This transforms the ink from a liquid to a solid, drying it instantly.
- Unlike traditional inks where the solvent evaporates, the photoinitiators are consumed during the curing process in UV inks. This means there is no shrinkage or loss of volume as the ink cures.
- Components of UV-Curable Inks
UV-curable inks are composed of four main components:
- Monomers - Provide properties like flexibility and hardness. They also control viscosity.
- Oligomers - Act as resins and adhesives to bond the ink to the substrate.
- Photoinitiators - Absorb UV light and initiate polymerization.
- Pigments - Provide color to the ink. The pigments are ground into nanoparticles for optimal color development and to prevent nozzle clogging issues.
In addition, UV inks may contain other additives like surfactants, stabilizers, and adhesion promoters depending on the specific formulation and application.
Advantages of UV Curable Inks
UV-curable inks offer several benefits that make them advantageous over traditional solvent and water-based inks:
- Instant drying - The ink dries instantly when exposed to UV light, allowing immediate further processing or handling of the printed material. This increases productivity in printing facilities.
- Superior print quality - As the ink remains on the surface and does not absorb into the substrate, the result is more vibrant, intense, and glossy colors. UV inks also allow printing finer details and gradients.
- Versatile substrate compatibility - UV inks can be used to print on a wide variety of substrates including plastics, metals, glass, wood, ceramics, and more.
- Durability - UV-cured prints are highly scratch, abrasion, and chemical resistant due to the cross-linking of polymers. They also have excellent weather resistance and lightfastness.
- Lower VOC emissions - UV inks contain little or no volatile organic compounds (VOCs) and solvents, making them more environmentally friendly.
- No dot gain - Unlike traditional inks, there is negligible dot gain as UV inks do not absorb into the substrate. This allows excellent color consistency.
- Reduced costs - The instant drying eliminates the need for drying equipment. UV inks also reduce waste and energy consumption.
Applications of UV Curable Inks
The unique properties of UV-curable inks make them suitable for a wide range of printing applications across many industries:
- Signage - Durable and weather resistant UV-cured prints are ideal for both indoor and outdoor signage.
- Labels - Excellent print quality and chemical/scratch resistance suit UV inks for label printing on various substrates.
- Packaging - Superb bonding to non-porous substrates allows UV inks to print directly onto glass, metal, and plastic packaging.
- Commercial Printing - Instant drying enables high-speed printing with UV inks on paper and carton boards.
- 3D Printing - UV-curable resin is commonly used in stereolithography and DLP 3D printers to create 3D objects layer by layer.
- Electronics - UV-curable conductive inks are used to print circuit boards, RFID antennas, and other electronic components.
- Medical Devices - Durable and sterilizable UV-cured prints are used to mark surgical tools and medical devices.
- Decorative Printing - Excellent adhesion allows UV inks to print vibrant, durable images onto wood, glass, metal, and ceramics.
UV Curing Methods
There are several methods available for curing UV inks, with the most common being:
- Mercury arc lamps - One of the earliest methods, which use mercury vapor lamps to emit UV light. These are being phased out due to the toxicity of mercury.
- UV LED - UV LED lamps offer several advantages over mercury arc lamps including lower energy consumption, longer life, reduced heat emission, and the absence of mercury.
- UV laser - Powerful UV lasers provide pinpoint accuracy for curing but have high costs. They are used mainly for etching, cutting, and selective curing.
- E-beam curing - An electron beam is used to generate UV radiation which instantly cures the inks. E-beam curing produces no ozone but requires significant safety measures.
Formulating UV-Curable Inks
Formulating UV-curable inks is a complex process that requires carefully balancing the components to achieve the desired performance and print properties. Here are some key considerations:
- Viscosity - Affects jetting performance and is controlled via the monomer mix. Low viscosity UV inks are preferred for inkjet printing.
- Curing speed - Dependent on the type and concentration of photoinitiators. Faster curing allows higher print speeds.
- Adhesion - Promoted by optimizing the oligomer chemistry and use of adhesion promoters.
- Flexibility - Monomer selection controls the flexibility of cured prints. Important for printing onto flexible substrates.
- Weather/chemical resistance - Related to the degree of cross-linking and types of oligomers/monomers used.
- Color - Careful pigment dispersion is vital for optimal color development without nozzle clogging issues.
Extensive R&D, testing, and quality control are required to develop UV ink formulas that meet the required performance metrics.
Limitations of UV-Curable Inks
Despite the many benefits, UV-curable inks also come with some limitations:
- Higher costs - UV inks are more expensive compared to solvent and water-based inks. The printers also require integrated UV curing systems.
- Limited flexibility - Heavily cross-linked UV prints have less flexibility compared to other inks. Stretchable substrates may be problematic.
- Lightfastness issues - Some UV inks, particularly cyan and magenta pigments, are prone to fading with long-term light exposure.
- Toxicity - Skin exposure to uncured photoinitiators can cause irritation, requiring careful handling.
- Surface curing - As UV light only penetrates the surface, thick ink deposits may not cure fully.
- Substrate limitations - Performance varies on different materials. Porous, stretchy, and dark substrates are not ideal.
The Future of UV-Curable Inks
UV-curable ink technology continues to advance, expanding into new applications and improving print performance. Some key trends shaping the future of UV inks include:
- Inkjet optimization - Developing UV inks with very low viscosity and particle sizes suited for inkjet printing.
- LED curing - UV LED curing systems are becoming predominant due to their lower costs, energy efficiency, and design flexibility.
- 3D printing - UV-curable resins are being adapted for diverse 3D printing techniques beyond stereolithography.
- Sustainable raw materials - Biomass and plant-derived resources are being utilized as sustainable alternatives to petroleum-based chemicals.
- Smart inks - UV inks are being enhanced with special additives to impart electrical, thermal, optical, or biological properties.
- Hybrid UV formulations - Combining UV technology with other curing mechanisms (e.g. moisture curing) to obtain specific advantages.
- Inkjet digital textile printing - Ongoing R&D to develop UV-curable inks for direct printing onto textiles.
As technology progresses, UV-curable inks will continue to displace traditional inks in more and more printing applications across many industries.
Conclusion
UV-curable inks represent a major advancement in printing technology, offering instant curing and superior print quality on a wide range of substrates. The unique photopolymerization process enables several key benefits like instant drying, vibrant colors, fine details, and excellent durability. These advantages have led to the increasing adoption of UV inks for diverse applications across many industries.
While higher costs and toxicity require safety measures, the environmental benefits of lower VOC emissions are significant. Ongoing innovations in areas like LED curing, sustainable raw materials, and inkjet optimization will continue to expand the capabilities and applications of UV-curable inks. With their instant curing ability and excellent printed results on almost any substrate, UV inks are poised to displace traditional inks in many more printing processes in the future.